Sometimes I do woodworking demos at SCA events, and I have been wanting a less modern water source for sharpening than my plastic container. I was watching the animated film “Spirited Away” and I was like, “I need that bucket.”
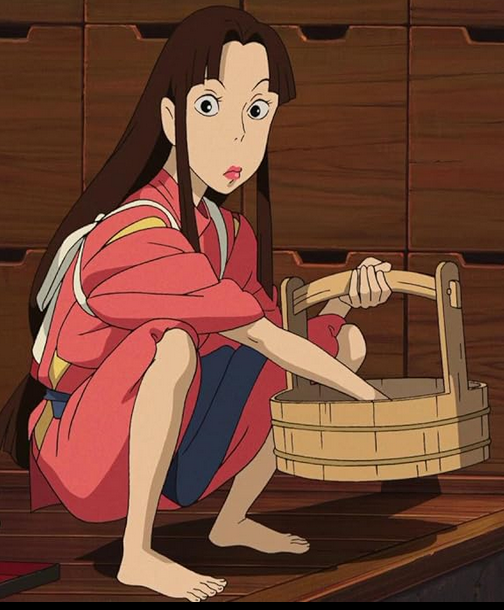
I think that in Japan, this low and wide type of bucket was basically used as a basket. In the movie, she has it full of candy (konpeito, basically little bumpy sugar balls) that she’s feeding to the soot sprites. I’ve seen large ones in other movies used to transport cooked rice.
I bought about twelve feet of cedar 1by6 (sold as 4/4 S3S) and planed it down to 3/4″. Then I cut 10 6″ long bits for the staves and 2 15″ long pieces for the handle staves. I tilted the table saw blade to 15 degrees and beveled one edge, then spun each piece around to both bevel the other edge and narrow each piece down to 3+7/8″ wide (on the wider side). Switching the table saw over to a dado stack, I cut a 3/4″ wide by 3/8″ deep dado on the interior of each piece, to accept the floor of the bucket.
I used the band saw to shape the handle staves, then cut the through-mortises on the drill press and chiseled them square.
The floor of the bucket is cut from three pieces of cedar that I edge-glued together and then shaped using a circle jig on the band saw. I cut that as a 14″ circle, but I wish I had gone up at least a quarter inch more.
I dry fit all the pieces using blue tape, so I could figure out how long the handle needed to be. Once I had that length, I sketched out the curve of the handle and cut the shape on the band saw. A bit of sanding smoothed away the blade marks.
Since I already had the pieces taped up, I could apply plenty of glue, roll the bucket up around the floor (inserting the handle at the right moment), and clamp it together with elastic bands. I should have used ratchet strapspn as that would have let me get them really tight. Since I knew cleaning dry glue off the inside would be a pain, I washed the squeeze-out off the interior before it could cure. I left the whole thing to dry overnight.
The next morning I removed the elastic and tape. I scraped the squeeze-out off the exterior, then sanded the angled edges of the exterior to round it up a bit. I drilled some holes in the handle tenons so I could secure them with pegs. To finish up, I tied some palm rope around the bucket with constrictor knots.
It leaked almost as fast as the hose could fill it, so I guess it’s not the best bucket anybody ever made, but it looks good, and I learned some lessons that will help me when (if) I make another one.
- Cut and shape the staves, then measure the dry fit to figure out how big the floor should be.
- Cut the dado to be a tight fit for the floor.
- Use ratchet clamps for a tight fit while the glue cures.
In Japan, they take pride that the joinery in their coopering (and boatmaking) is tight enough to be leakproof before it gets wet. The swelling makes it even tighter! I knew ahead of time that my joinery would not be up to Japanese level. Traditional buckets (and barrels) also have good quality hoops that keep the joinery tight as the wood swells. In Japan, making hoops by braiding strips of bamboo is a craft all on its own. I knew my rope hoops would be a little loose, and that I am not capable of metalworking at this level either, so glue it was.
I did not put any glue holding the bottom in place, because I knew that had to be free to swell. In my future tries to learn this craft, I will make the staves first, then measure to determine what size I need the floor to be. I’ll also leave the boards for the floor a little bit thicker, to match what is apparently a slightly over-width dado stack.
After a few days, I decided to seal the bottom of the bucket with clear finishing resin so that I could use it for its intended purpose. I sealed up the outside of the floor as best as I could with blue tape, then I poured in about 2 cups of mixed resin. I probably could have gotten away with only a cup of resin, since the hardened resin is pretty thick in the bucket now.
When it started to thicken, I brushed the resin up the sides of the bucket, sort of to make a plastic bucket inside. I knew the wood was porous, and I was hoping enough resign would soak in that the wood bucket and the plastic surface would be fully bonded together. One thing I did not take into account was that these pores are all full of air. Since the resin heats up as it cures, the air expanded and bubbled up through the resin. I did not get a perfectly clear layer of plastic in the bottom of the bucket, but it did seal everything up as hoped.
It looks good overall though, and I am happy with it. Once you get some water in it, you can’t really tell the difference between bubbly resin and bubbly water. I have my bucket and it really does look like the inspiration. One commentator suggested that I make two more. The theory is that by the time I make the third one, I’ll have all the problems worked out and the third one will be perfect. That will have to wait for Spring, but I just might do it.