Eleven years ago, I made this hexagonal bento box in a class taught by Pittsburgh’s Tadao Arimoto. At the time, I did not know much about making bento lunches, so the box mostly sat on a shelf as a display piece. It waited patiently for me to expand my studies of Japanese culture to include food, and for me to start shopping at the Tokyo Japanese grocery enough to develop a menu for lunch. Back in 2019, I started making bento lunches to eat at work, and I discovered that the box was not sealed! I got salad dressing all over the tablecloth, and had to use plastic bento boxes for my lunch.
A year or two ago, I sanded the inside and outside of the box to smooth out the uneven epoxy surface. The box sat in this state for a couple of years, still waiting for me to make time for it. This summer, I finally cleared off the workbench for a couple of days so that I could mix up some epoxy and refinish the box.
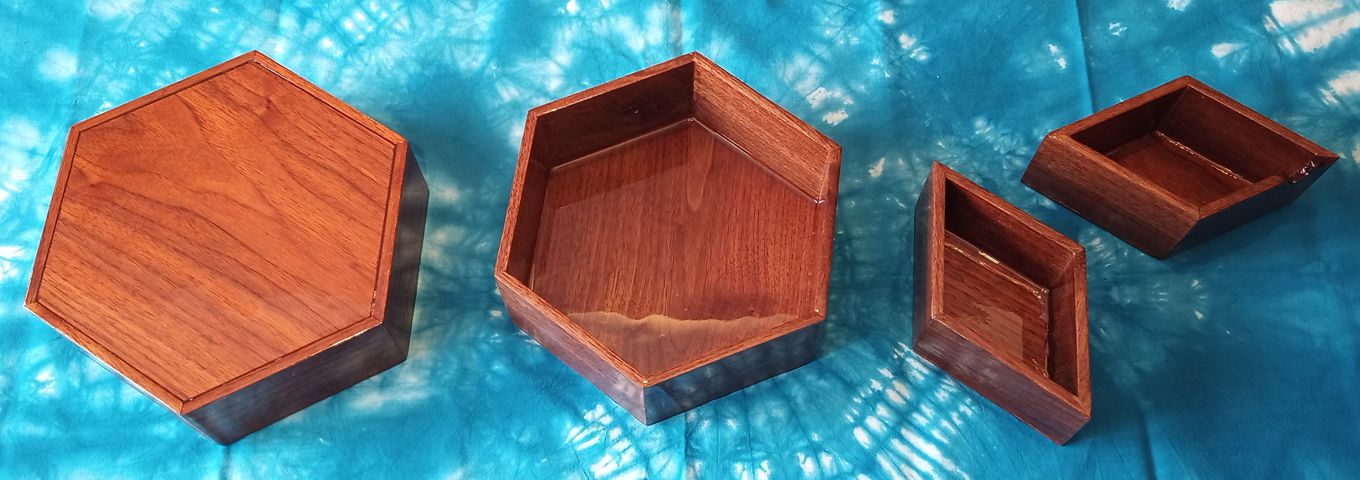
It’s completely sealed now. I could probably take soup in it. The lid edges are almost the full height of the box, so it might not even spill very much if tipped. Even though I don’t go into the office at all these days, I made lunch at home and served it to myself in this box because I believe you should always let things fulfill their purpose.
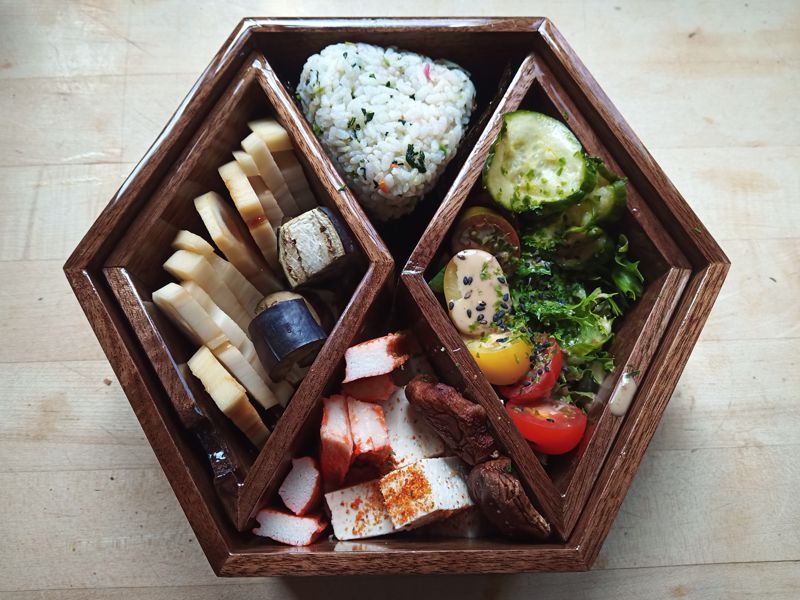